Revenue Generation and Economic Resilience in Continuous Tire Pyrolysis System
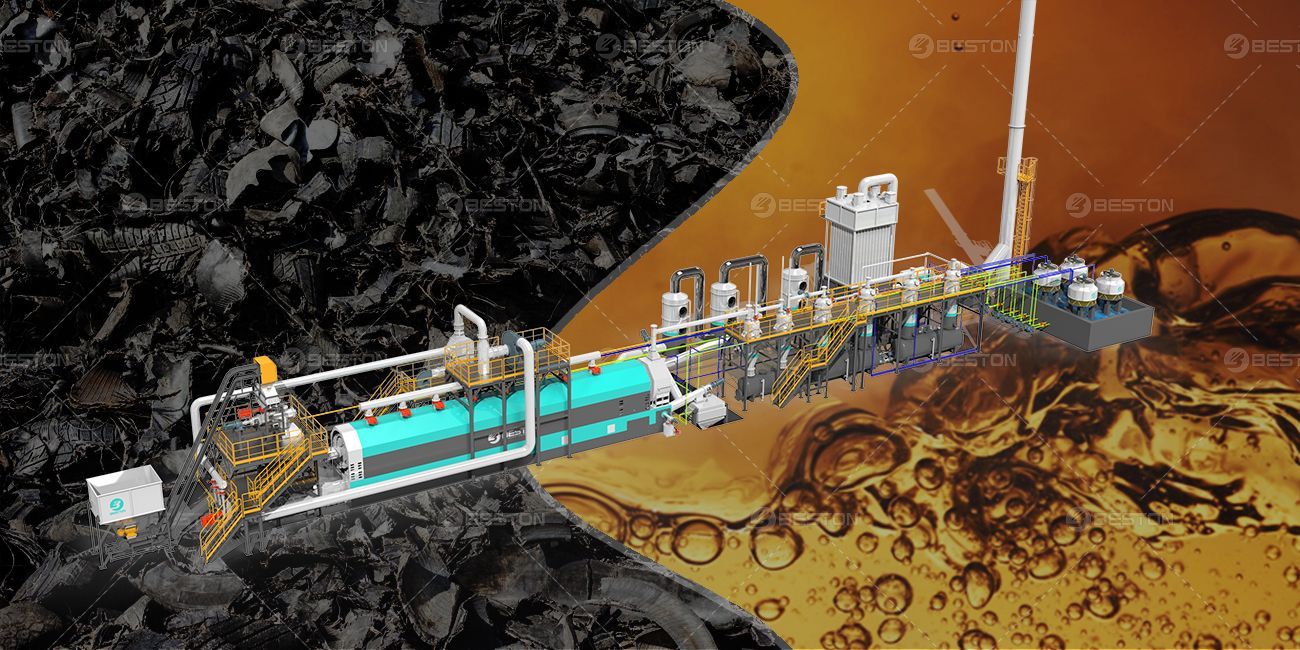
End-of-life tires (ELT) represent a growing environmental liability. However, through the deployment of a continuous pyrolysis plant, they can be repurposed into commercially valuable outputs. Unlike batch models, continuous tire pyrolysis maximizes feedstock throughput, energy efficiency, and uptime—key parameters in enhancing profitability.
Operational Continuity as a Revenue Multiplier
A continuous tyre pyrolysis plant functions on an uninterrupted feed-discharge cycle, eliminating start-stop inefficiencies common in batch systems. By maintaining stable thermal conditions and eliminating downtime between cycles, facilities can process significantly more material over a given time horizon.
- 24/7 uptime means higher annual throughput.
- Reduced thermal shock cycles lower maintenance frequency and extend component lifespan.
- Automated feeding and discharging reduce manual intervention and associated labor costs.
For a standard line processing 20 tons of tires daily, continuous operation enables recovery of over 7,000 tons per year, creating predictable and scalable revenue streams.
Multi-Output Product Portfolio
Tire pyrolysis yields four primary byproducts: pyrolysis oil, carbon black, steel wire, and non-condensable gas. Each has specific market applications and pricing structures.
- Pyrolysis oil (45–50% yield) serves as a fuel alternative or industrial heating oil. With mild upgrading, it can enter the bunker fuel or refinery feedstock market.
- Recovered carbon black (30–35%) is utilized in pigment, asphalt additive, and rubber manufacturing sectors. Micronization and pelletization significantly increase its market value.
- Steel wire (10–15%) is extracted and sold to scrap dealers, particularly in regions with active ferrous recycling infrastructure.
- Non-condensable gas powers tyre to oil plant, displacing external energy inputs and reducing fuel expenditures.
The diversification of outputs cushions operators from price volatility in any single commodity stream.
Input Sourcing and Market Arbitrage
Tires are widely available waste materials. In many jurisdictions, governments and waste handlers offer tipping fees or rebates for their processing, effectively converting feedstock acquisition into a revenue event.
- Tipping fee regimes provide upfront revenue for accepting tires, common in Europe and parts of North America.
- Circular economy mandates increasingly compel tire manufacturers to collaborate with licensed recyclers, ensuring consistent feedstock flow.
Combining waste diversion incentives with product revenue allows for dual-income monetization models.
ROI accelerates further when the pyrolysis plant is integrated with downstream refining, pelletizing, or power generation modules.
Regulatory and Carbon Offset Leverage
In the evolving policy landscape, continuous pyrolysis plants align with both waste reduction mandates and carbon abatement strategies. Valorization of ELTs reduces landfilling and uncontrolled burning, generating carbon offset potential.
- Carbon credit registration (via voluntary markets or government schemes) can monetize emissions avoided through tire recycling.
- Compliance with Extended Producer Responsibility (EPR) frameworks may position the plant as a certified downstream recycler, attracting OEM partnerships.
Environmental alignment enhances project bankability, investor attractiveness, and long-term market access.