Optimal Geographies for Tire Pyrolysis Oil Production Deployment
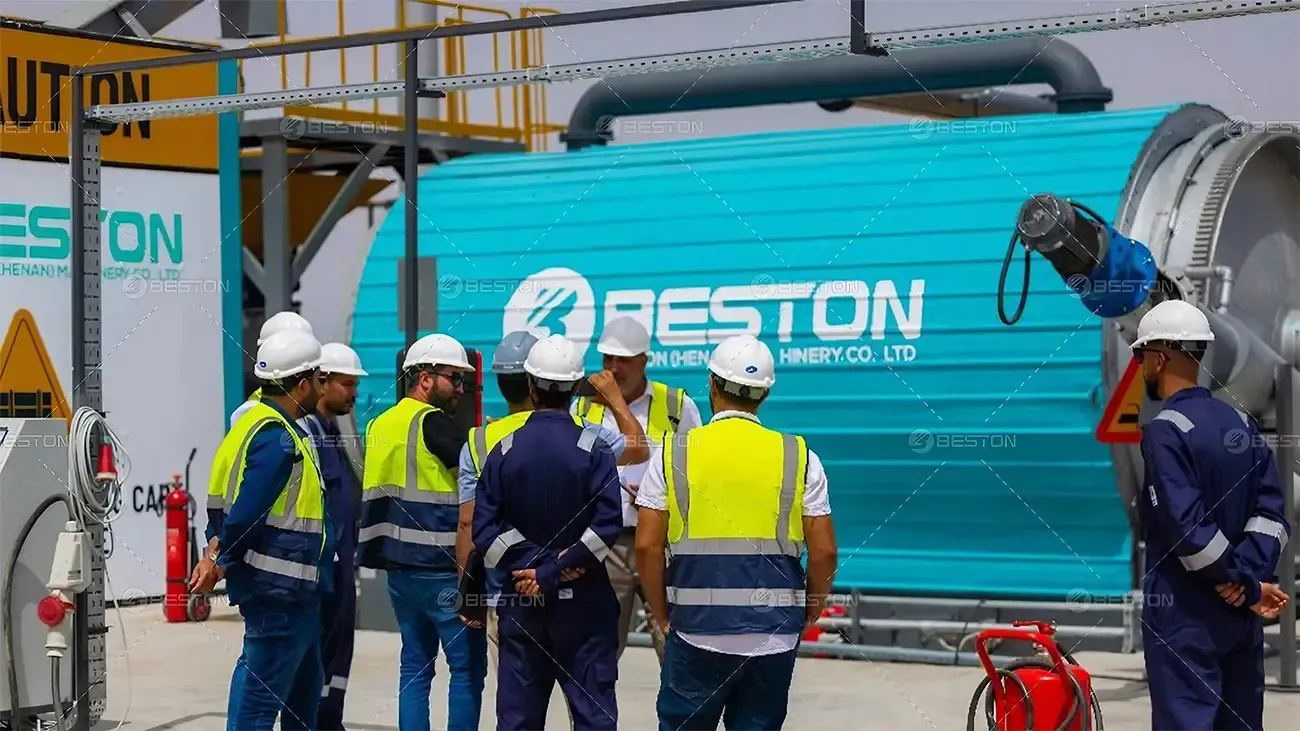
The global stockpile of end-of-life tires (ELT) has escalated into a persistent environmental and logistical burden. While traditional landfilling and incineration present ecological risks, pyrolysis offers a thermochemical alternative—converting rubber waste into marketable tire-derived oil, carbon black, and gas. Yet, the success of a pyrolysis plant is strongly tied to strategic siting. Regions with concentrated feedstock, regulatory flexibility, and downstream consumption channels offer superior viability for tire pyrolysis oil production.
Automotive Manufacturing and Disposal Clusters
Countries with high vehicle ownership rates and established auto-manufacturing bases generate consistent volumes of used tires. North America, Germany, Japan, and South Korea are prime examples. Within these territories, urban-industrial belts such as the U.S. Rust Belt or the Tokai region of Japan offer synergistic value chains.
Decommissioned tires from automotive service centers and scrappage programs can be aggregated with minimal transport cost. Co-locating a continuous pyrolysis plant near tire shredding facilities ensures a steady, pre-processed rubber feedstock stream. Additionally, proximity to automotive suppliers and lubricant blenders enhances the commercial outlet for recovered pyrolysis oil and carbon black.
Port Cities with Import-Export Recycling Loops
Large coastal metropolises such as Rotterdam, Shanghai, Durban, and Los Angeles function as nodes for global material flow. Inbound used-tire shipments—often from developing countries or OEM surplus—provide surplus feedstock. Port-adjacent industrial zones offer tax incentives, robust energy supply, and tank storage infrastructure.
Tire pyrolysis oil produced in these regions can be readily exported as industrial fuel or cracked into light distillates by nearby refineries. Marine fuel substitution also presents a viable offtake strategy, especially in jurisdictions navigating IMO 2020 sulfur regulations.
Developing Nations with High Scrap Tire Accumulation
Emerging economies frequently experience tire waste accumulation due to limited end-of-life management frameworks. Countries like Nigeria, India, Brazil, and Indonesia present acute waste challenges but also high-value opportunities for pyrolysis deployment.
The availability of low-cost labor, coupled with significant informal tire collection networks, reduces operational expenditure. When integrated with government clean-up initiatives or waste-to-energy mandates, a tire pyrolysis plant can serve both environmental remediation and local fuel substitution needs. In these markets, tire-derived oil is often used as a direct replacement for furnace oil in brick kilns and boilers.
Regions with Restricted Landfill Access
Land-constrained geographies, including parts of the European Union, Taiwan, and island nations such as Sri Lanka or the Philippines, impose stringent landfill bans or taxes on tire disposal. These restrictions accelerate the demand for alternative processing routes, making pyrolysis not only attractive but necessary.
Local policy frameworks typically support pyrolysis through tipping fees, feed-in tariffs, or green fuel credits. This regulatory alignment ensures predictable revenue channels, especially when carbon intensity reductions are monetized via compliance or voluntary markets.
Oil and Gas Regions Seeking Waste-Derived Fuel Blends
Oil-producing zones with refining infrastructure—such as Alberta, Texas, the Persian Gulf, and Eastern Siberia—can efficiently absorb pyrolysis oil into downstream blending systems. These regions benefit from existing hydrocarbon transport, storage, and combustion systems.
Deploying a pyrolysis plant in such locations enables tire waste to be repurposed into refinery feedstock, bunker fuel, or even gasifier-compatible liquids. Co-processing in fluid catalytic crackers (FCCs) or hydrocrackers can further enhance the yield profile while meeting environmental emissions thresholds.
Mining and Heavy Industry Zones with Onsite Energy Demand
Remote mining and cement operations in regions like Western Australia, northern Chile, or South Africa require uninterrupted thermal and electrical energy. Transporting conventional fuel to these sites is costly and logistically complex.
Onsite tire pyrolysis plants—fed by local stockpiles or imported baled tires—offer a decentralized fuel generation model. The gas and oil outputs can offset diesel consumption in generators, while the recovered steel can be sold or reintegrated into local smelting operations.
Prioritized Siting Criteria for Long-Term Viability
Optimal deployment of tire pyrolysis facilities requires harmonizing feedstock logistics, downstream compatibility, and environmental compliance. High tire density zones, industrial energy users, and policy-aligned jurisdictions present the most favorable conditions. Strategically siting a pyrolysis plant in such areas ensures sustainable throughput, minimized waste transport, and economically viable oil recovery from a persistently underutilized resource.