Key Benefits of Continuous Plastic Pyrolysis Technology
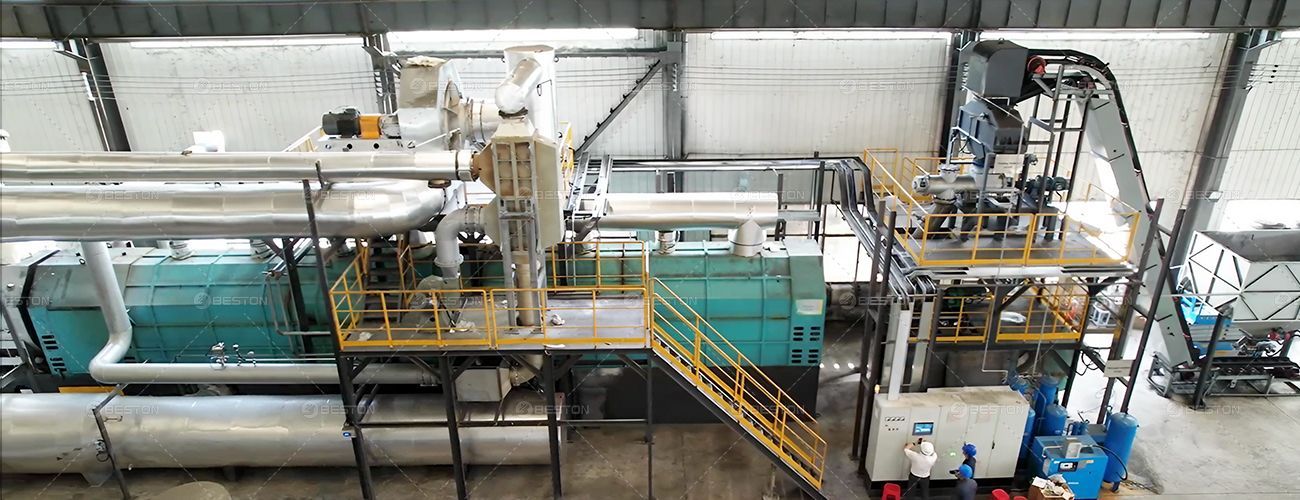
The growing accumulation of plastic waste poses a significant environmental challenge globally. In response, continuous plastic pyrolysis technology has emerged as a promising solution, offering an efficient and scalable approach to managing plastic waste. By converting plastics into valuable resources such as fuel oil, carbon black, and gas, this technology not only reduces plastic pollution but also provides economic benefits. A pyrolysis plant designed for continuous operation streamlines waste processing, enabling improved productivity and energy efficiency.
Enhanced Operational Efficiency
The most notable advantage of continuous plastic pyrolysis plant lies in its operational efficiency. Unlike batch pyrolysis systems, which require periodic loading and unloading of material, continuous pyrolysis plants operate nonstop. This design significantly enhances throughput, making it ideal for large-scale operations. Plastic waste is continuously fed into the reactor, where it undergoes thermal decomposition in the absence of oxygen, breaking down into usable byproducts like fuel oil and gas.
The continuous process also minimizes labor input, as operators only need to monitor and adjust parameters rather than frequently halt production to remove finished material. This leads to reduced operational downtime and labor costs, ultimately increasing the profitability of pyrolysis projects. Furthermore, continuous pyrolysis systems offer a higher degree of process control and automation, allowing for more precise adjustments to temperature, pressure, and feed rate to optimize output.
Higher Throughput and Scale
For businesses looking to scale up plastic waste recycling, a continuous plastic pyrolysis plant is an excellent choice. The ability to process large volumes of plastic waste consistently allows companies to maximize production while maintaining high efficiency. Whether for recycling plastic from industrial sources or municipal waste streams, continuous pyrolysis can handle a variety of feedstocks, from polyethylene to polypropylene and other common plastic types.
The scalability of continuous pyrolysis systems is particularly advantageous in regions with high levels of plastic waste generation. By upgrading or expanding existing facilities with continuous pyrolysis units, businesses can effectively address waste management needs without significant increases in operational complexity. This scalability ensures that larger volumes of plastic can be processed without sacrificing quality or efficiency.
Consistent Product Quality
In continuous pyrolysis technology, the ability to maintain consistent operating conditions results in more uniform products. The controlled environment inside the pyrolysis plant helps ensure that each batch of plastic waste is processed in the same manner, producing high-quality fuel oil, carbon black, and other byproducts. This uniformity is crucial for industries that rely on these byproducts, such as the energy and materials sectors.
Fuel oil produced from pyrolysis can be used in various applications, including as a substitute for conventional fuels in industrial boilers or engines. Carbon black, another key byproduct, is widely used in the production of rubber, inks, and coatings. Continuous operation ensures that these materials meet the required specifications, making them valuable commodities in the marketplace.
Lower Environmental Impact
Continuous plastic pyrolysis technology contributes to reducing the environmental impact of plastic waste disposal. Traditional methods like landfilling and incineration release harmful chemicals into the environment and contribute to pollution. In contrast, pyrolysis offers a cleaner, more sustainable alternative. The process is environmentally friendly as it prevents plastic waste from accumulating in landfills and avoids toxic emissions associated with incineration.
Moreover, the carbon footprint of continuous pyrolysis plants is minimized by the use of energy recovery systems. The gas produced during the pyrolysis process can be captured and used as fuel to power the reactor, reducing the need for external energy sources. This integrated energy management system ensures that the plant operates with maximum energy efficiency, further lowering its environmental impact.
Economic Viability
Investing in continuous plastic pyrolysis technology also offers significant economic advantages. The sale of byproducts such as fuel oil and carbon black provides a steady revenue stream, making the pyrolysis plant a profitable investment. Fuel oil, for example, can be sold to industries in need of alternative energy sources, while carbon black is in demand across various industries, particularly in tire manufacturing.
The reduced operational costs associated with continuous pyrolysis, including lower labor and maintenance expenses, also contribute to the plant's overall economic viability. Additionally, as the technology matures and economies of scale are realized, the capital costs of installing and operating a continuous pyrolysis plant are expected to decrease, making it a more accessible option for a wider range of businesses and municipalities.
Flexibility in Feedstock
One of the key advantages of continuous pyrolysis technology is its ability to handle a wide variety of plastic feedstocks. Pyrolysis plants can process different types of plastic, including polyethylene, polypropylene, and polystyrene, with minimal pre-treatment. This flexibility makes the technology well-suited to regions with diverse waste streams, as it can accommodate varying types of plastic waste without the need for extensive sorting or processing.
Furthermore, continuous pyrolysis plants can be integrated with other waste management technologies, such as mechanical recycling or waste-to-energy systems, to further enhance feedstock flexibility. This adaptability allows businesses to customize their operations to meet local waste disposal needs and further streamline the recycling process.
Long-Term Sustainability
As the global demand for plastic continues to rise, finding sustainable solutions for managing plastic waste is increasingly important. Continuous pyrolysis technology offers a long-term solution that aligns with circular economy principles. By converting plastic waste into valuable byproducts, pyrolysis supports resource recovery and reduces the need for virgin materials in manufacturing processes.
This technology also contributes to a more sustainable waste management model by diverting plastic from landfills and incinerators, which are often costly and environmentally harmful. With the potential for higher efficiency, consistent output, and lower environmental impact, continuous pyrolysis provides a viable pathway toward sustainable plastic waste recycling.