Evolution of Thermal Desorption Technology in Oil Sludge Treatment
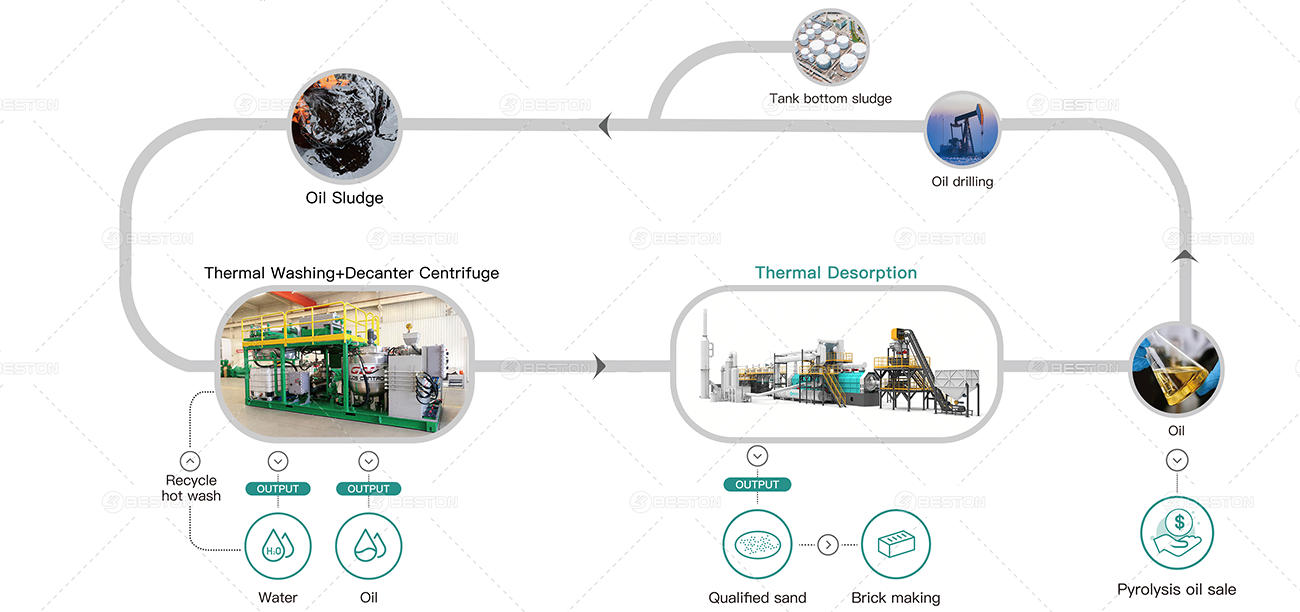
The management of oil-contaminated waste has long posed an environmental and technical challenge for petroleum-producing regions. Among available solutions, thermal desorption has emerged as a principal method for hydrocarbon recovery and waste minimization. The trajectory of this technology—both in design and performance—has been shaped by tightening regulations, material science innovations, and the increasing demand for circular economy practices.
Early Thermal Approaches: Incipient Principles
Initial concepts of thermal desorption were rooted in basic volatilization techniques. Primitive systems operated in batch mode with minimal temperature control, targeting surface-level hydrocarbons through direct heating. These units were limited in scope, processing capacity, and contaminant profile. Typically deployed in remedial projects, they lacked the scalability and precision required for industrial applications.
These early designs, though rudimentary, demonstrated that hydrocarbons could be effectively separated from oily matrices at elevated temperatures without combustion. The challenge was to elevate throughput while reducing energy consumption and meeting evolving emission standards.
First-Generation TDU Systems: Direct-Heating and Low Retention
By the 1980s, first-generation TDU (Thermal Desorption Unit) systems began to incorporate controlled temperature zones and enhanced residence time. Direct-fired rotary kilns and screw conveyors were commonly adopted. These systems operated within 300°C–450°C and were capable of treating oil-based drill cuttings, refinery sludge, and tank bottom residues.
Key features of this generation included:
- Low to moderate throughput (1–5 tons per hour)
- Manual feed mechanisms
- Limited vapor capture or treatment
While effective in removing light to medium-chain hydrocarbons, these units had high energy intensity and often released volatile organic compounds (VOCs) into the atmosphere. Environmental agencies soon imposed stricter emissions controls, pushing the need for more advanced systems.
Second-Generation Advancements: Indirect Heating and Modularization
A technological leap occurred in the 1990s and early 2000s with the development of indirectly heated TDU systems. These designs introduced external heat sources, such as electric heaters or thermal oil, to minimize direct contact between flame and waste. The approach significantly reduced the risk of oxidation and ensured better control of thermal profiles.
Improvements in this phase included:
- Modular designs for mobile and offshore use
- Enhanced vapor recovery units with condensers and scrubbers
- Greater automation and process stability
Increased focus was also placed on recovering hydrocarbons for reuse rather than destruction. Systems began incorporating condensate recovery lines capable of producing reclaimed oil suitable for industrial burning or re-refining.
Third-Generation Systems: High-Efficiency and Multi-Phase Treatment
The modern era of TDU technology is defined by high-throughput, continuous systems capable of processing complex multi-phase waste. These include centrifuge-separated oil sludge, emulsified mixtures, and materials with high water and solids content.
Contemporary TDU designs feature:
- Operating temperatures of 450°C–650°C
- Heat recovery systems to minimize fuel use
- Advanced PLC-controlled feedback loops
- Integrated pre-treatment and vapor condensation trains
The integration of mechanical dewatering, indirect thermal separation, and post-treatment polishing stages has elevated recovery efficiency. Hydrocarbon recovery rates can now exceed 90%, with residual solid outputs compliant with hazardous waste criteria in many jurisdictions.
Environmental Integration and Global Deployment
The expansion of thermal desorption technology into global oil markets—particularly in the Middle East, North Africa, and Southeast Asia—has been accelerated by the need to address legacy waste and ongoing refinery operations. Regulatory frameworks such as the Basel Convention and national waste classification systems have pressured operators to adopt low-emission, recoverable technologies.
TDU systems are now often designed with:
- Carbon capture readiness
- Zero-liquid discharge (ZLD) compatibility
- Compliance with EU BAT (Best Available Technique) references
This shift marks the convergence of environmental stewardship with economic return. Operators are no longer treating sludge as disposable waste, but as a resource stream containing valuable hydrocarbons and reusable inert materials.
Looking Ahead
Thermal desorption is no longer a single-technology solution but part of an integrated waste valorization platform. Innovations in hybrid heating, AI-based control, and low-carbon fuel integration will continue to redefine TDU performance standards.
In the broader context of sustainable oilfield operations, thermal desorption remains a critical link between regulatory compliance and operational profitability—serving both legacy waste treatment and modern production waste streams.