Influence of Raw Material Fluidity on Biochar Production
- By Beston Charcoal
- •
- 21 Nov, 2024
- •
The production of biochar relies significantly on the characteristics of raw materials used in the process. Among these, the fluidity of the material plays a critical role in determining efficiency, quality, and consistency in biochar yield. Fluidity encompasses factors like particle size, moisture content, and physical flow properties, all of which interact with biochar production equipment during the thermal conversion process.
Defining Fluidity in Biomass Context
In the context of biomass conversion, fluidity refers to the ease with which raw materials can be handled, transported, and processed within biochar production equipment. Materials with high fluidity flow more smoothly through feed systems, reactors, and discharge mechanisms. Conversely, low-fluidity materials often require specialized pre-treatment to mitigate clogging, uneven heating, or energy inefficiencies.
Factors Influencing Raw Material Fluidity
Particle Size and Shape
Finely ground biomass, such as sawdust or powdered agricultural residues, tends to have higher fluidity. Uniform particle size allows consistent feeding into reactors and promotes even pyrolysis. Irregular or coarse particles can obstruct mechanical feeding systems and create inconsistencies in heating rates.Moisture Content
Excessive moisture impairs material fluidity by increasing cohesiveness, which leads to clumping during feeding. High-moisture materials often require drying stages before entering biochar production equipment, adding to energy and time costs. Optimally, raw materials should have a moisture content below 20% for efficient processing.Material Composition
Fibrous or resinous biomass may exhibit reduced fluidity due to its tendency to stick or bind during transportation and pyrolysis. Agricultural residues with higher lignin or cellulose content generally maintain better structural integrity, enhancing their flow properties.Bulk Density
Lightweight, low-density materials often display irregular flow patterns, necessitating adjustments in feeding systems. Denser biomass feeds more consistently but may pose challenges in energy-intensive grinding or transport mechanisms.
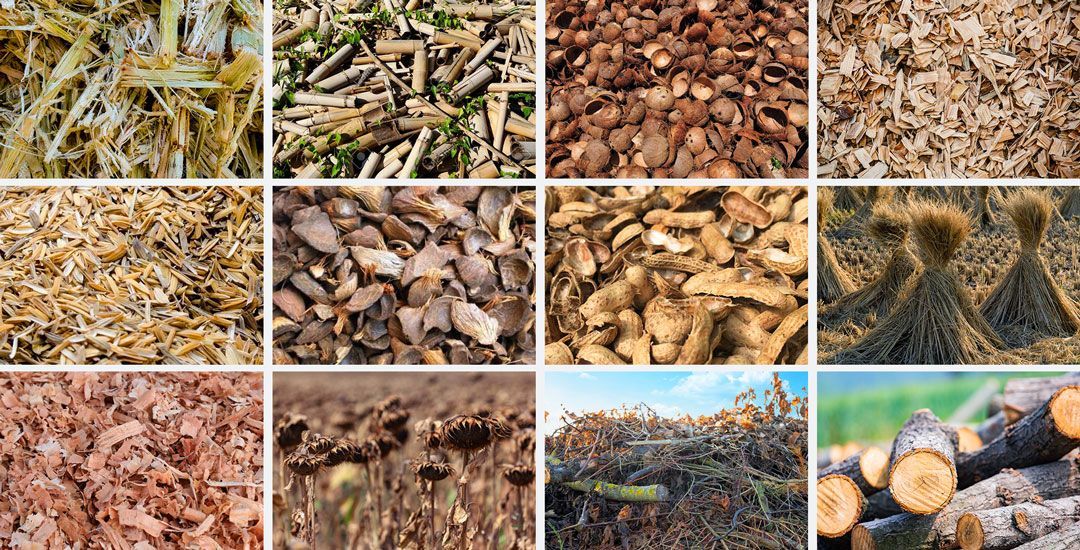
Impacts on Biochar Production Efficiency
Raw material fluidity directly affects several operational and output parameters in biochar production:
Reactor Throughput
Poor fluidity slows down the feed rate, limiting the overall throughput of biomass pyrolysis plant. Blockages or inconsistent feeding can lead to operational downtime, impacting productivity.
Thermal Efficiency
Fluidity influences the contact between biomass and heating surfaces. Uniform flow ensures consistent thermal exposure, while irregular movement can create hotspots, resulting in incomplete pyrolysis or char with heterogeneous properties.
Quality of Biochar
Materials with optimal fluidity produce biochar with uniform porosity, carbon content, and ash levels. Poorly flowing materials may lead to uneven carbonization, affecting the biochar's application potential, particularly in soil amendments or carbon sequestration.
Mitigation Strategies for Low-Fluidity Materials
Pre-Processing Techniques
- Grinding and Shredding: Reducing particle size improves flow characteristics and facilitates consistent feeding.
- Drying: Lowering moisture content through mechanical or thermal drying enhances material movement.
- Pelletizing: Compacted pellets exhibit improved bulk density and flowability, making them suitable for large-scale equipment.
Equipment Design Modifications
Biochar production equipment can be customized to handle low-fluidity materials effectively. Vibratory feeders, auger systems, or adjustable hopper designs help manage material flow issues. Reactor designs with dynamic agitation mechanisms also ensure consistent thermal exposure.Blending Materials
Mixing low-fluidity biomass with more flowable materials can improve overall handling properties. This approach is particularly useful for facilities processing diverse agricultural residues.
Different Material Fluidity
High-Fluidity Feedstocks
Agricultural residues like rice husks and wood chips exhibit high fluidity, requiring minimal pre-treatment. Their consistent feeding and pyrolysis result in high-quality biochar with predictable characteristics.
Low-Fluidity Feedstocks
Biomass such as wet food waste or fibrous coconut husks often poses challenges in feeding and pyrolysis. Pre-treatment through drying and blending significantly enhances their processability, enabling efficient biochar production.