Economic Viability of Rice Husk Biochar Production Projects
- By Beston Charcoal
- •
- 24 Apr, 2025
- •
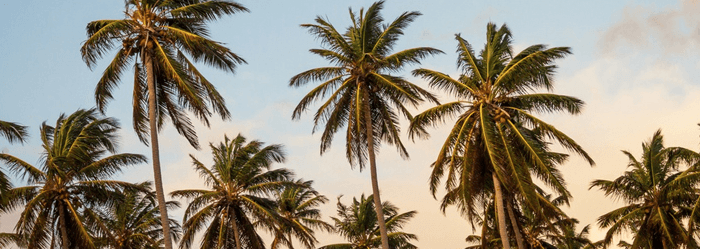
Rice husk, a by-product of rice milling, presents a significant opportunity for conversion into value-added products. Among the most efficient applications is its transformation into biochar through thermal decomposition. This process not only provides a method for biomass waste management but also offers a scalable economic opportunity. With growing demand for soil amendment solutions and sustainable agriculture, rice husk biochar production is garnering increased interest from both private and public sectors.
Capital and Operational Framework
The core equipment necessary for this transformation is the biochar machine, which operates via pyrolysis—an oxygen-limited process that thermochemically decomposes organic material. These systems are modular, with production capacity ranging from small-scale rural models to industrial-grade units.
Initial capital expenditure includes the cost of the biochar machine, site development, feedstock preparation systems, and ancillary infrastructure such as gas condensers and emission treatment units. Depending on capacity, the investment range varies widely, but operational cost efficiency often offsets the initial outlay within a reasonable payback period.
Operating expenses encompass raw material handling, labor, maintenance, and energy inputs. However, due to the self-sustaining nature of pyrolysis—where syngas generated in the process can be redirected to fuel the reactor—the energy costs are markedly reduced, improving net operating margin.
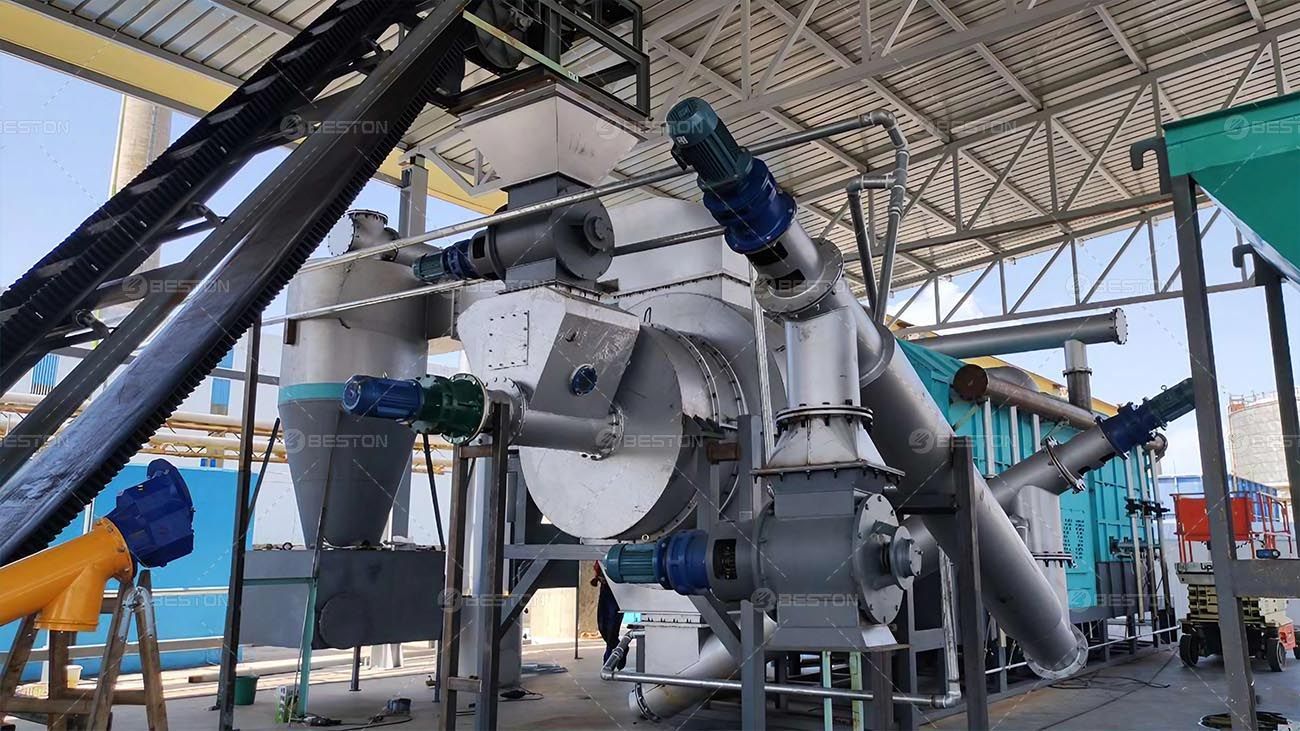
Revenue Stream Diversification
The economic return of a rice husk biochar project is primarily derived from multiple revenue-generating products:
1. Biochar Sales
The primary output, rice hull biochar, is in high demand as a soil conditioner. Its porous structure improves water retention, enhances microbial activity, and sequesters carbon in agricultural soils. These attributes align with the goals of climate-smart agriculture, boosting market appeal.
In markets where carbon trading mechanisms are active, biochar qualifies for carbon credits due to its carbon-negative lifecycle. This generates an additional revenue stream, often denominated in certified emission reductions (CERs) or voluntary emission reduction (VER) credits.
2. Syngas Utilization
During pyrolysis, volatile gases—mainly methane, hydrogen, and carbon monoxide—are released. These can be combusted in a secondary chamber to provide thermal energy for the biochar machine or used to power generators. In some models, excess electricity can be sold back to the grid, providing another avenue for financial return, especially in regions with favorable feed-in tariff policies.
3. Wood Vinegar and Bio-oil
Additional by-products such as wood vinegar and bio-oil are marketable in niche segments. Wood vinegar is used in pest control and as a growth stimulant in organic farming, while bio-oil, though less stable than fossil-derived oils, is gaining traction as a renewable industrial fuel.
Feedstock Economics
Rice husk, often available at minimal or no cost in rice-producing regions, offers a low-cost input for biochar production. In some cases, mills pay to dispose of husk waste, effectively creating a negative cost feedstock. This drastically improves the economic profile of the project.
The abundance and seasonality of rice husk must be considered in capacity planning. Establishing feedstock supply agreements with milling facilities ensures consistent input flow and mitigates supply-chain interruptions.
Environmental and Policy Incentives
Many governments provide fiscal incentives to promote biomass-to-energy conversion technologies. These include tax rebates, equipment subsidies, and low-interest green loans. Additionally, grants and soft funding from climate finance institutions may be available, particularly when the project demonstrates tangible carbon sequestration and supports local agricultural resilience.
Environmental compliance is crucial, with emission controls being a significant consideration in project design. Modern biochar machines are equipped with scrubbers and condensers to ensure that volatile organic compounds and particulate emissions are within regulatory limits.