Comparative Analysis of Tire and Oil Sludge Pyrolysis Processes
- By Beston Charcoal
- •
- 13 May, 2025
- •
Pyrolysis technology has diversified significantly in recent years, adapting to various feedstocks with unique chemical properties and operational requirements. Among the most commercially viable applications are tire pyrolysis and oil sludge pyrolysis. Both processes rely on thermal decomposition under anaerobic conditions, yet they diverge in critical aspects—ranging from feedstock composition and pretreatment needs to end-product yield and reactor configuration. An in-depth examination reveals how these differences shape pyrolysis plant design, process economics, and environmental outcomes.
Feedstock Characteristics
The first major point of divergence lies in the intrinsic nature of the feedstocks. Scrap tires consist primarily of synthetic rubber, carbon black, steel, and various chemical additives. This composition yields high calorific value and a relatively stable feedstock matrix. In contrast, oil sludge is a heterogeneous mix derived from petroleum refining processes. It contains a combination of water, hydrocarbons, heavy metals, and solid particulates.
Due to this disparity, tire pyrolysis typically exhibits greater consistency in thermal decomposition behavior. Oil sludge, however, presents challenges such as high moisture content and chemical variability, requiring more sophisticated preprocessing systems including dewatering and homogenization units.
Reactor Design and Process Optimization
A tyre pyrolysis plant commonly employs rotary kiln or batch-type reactors. These systems offer sufficient residence time and agitation to ensure complete devolatilization of the rubber matrix. The operation is relatively robust, accommodating the rubber’s elastic properties and metal content with minimal disruption.
Oil sludge pyrolysis, on the other hand, often necessitates a more controlled reactor environment. Fluidized bed and auger reactors are frequently utilized to handle the slurry-like consistency of the material. Precise thermal control and feedstock injection mechanisms are critical to maintain reactor stability and avoid fouling or coking of internal surfaces.
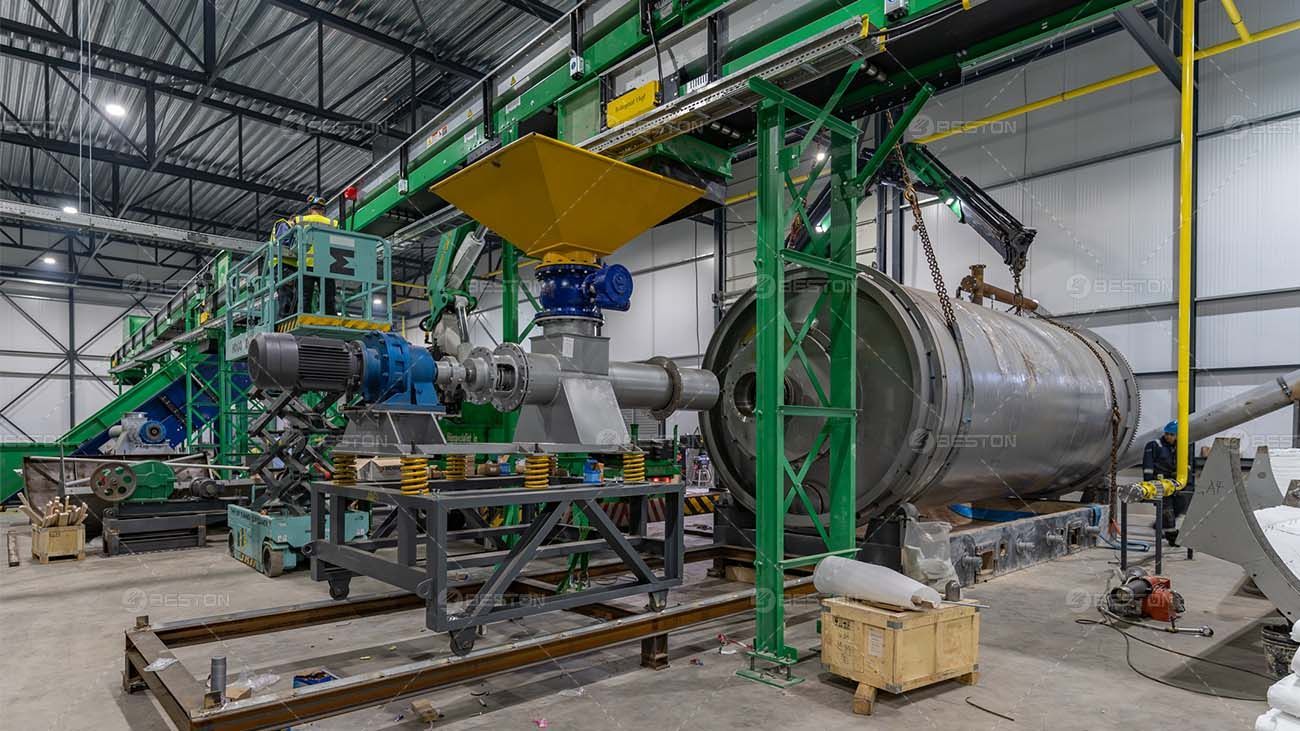
Product Composition and Yield
The end-product profile is another point of significant contrast. Tire pyrolysis typically produces pyrolytic oil (40–45%), carbon black (30–35%), steel wire (10–15%), and non-condensable gases (10–15%). These outputs have established downstream markets, particularly in fuel blending, pigment production, and metal recycling.
Oil sludge treatment yields a lower proportion of recoverable oil due to its inherent moisture and inorganic content. Typical outputs include pyrolytic oil (20–30%), solid residue laden with heavy metals (40–50%), and syngas (20–30%). The oil extracted often requires intensive post-treatment to meet fuel standards, while the residue may necessitate safe disposal or stabilization due to toxicity.
Emissions and Environmental Risk
In terms of emissions control, both processes must contend with volatile organic compounds (VOCs), sulfur compounds, and particulates. However, oil sludge pyrolysis poses greater environmental risk due to the potential release of heavy metals and polycyclic aromatic hydrocarbons (PAHs). Advanced gas scrubbing and residue stabilization systems are essential to meet environmental compliance.
Tire pyrolysis emissions are more predictable and easier to manage using conventional flue gas cleaning technologies. Moreover, the carbon content in the solid residue is typically inert, enabling safer handling or reuse.
Regulatory and Economic Considerations
From a regulatory standpoint, oil sludge is classified as hazardous waste in many jurisdictions. This imposes stricter permitting, operational, and disposal requirements. It also increases compliance costs and limits market entry for smaller operators.
Conversely, tires are generally categorized as non-hazardous waste, enabling more flexible deployment of pyrolysis plant infrastructure. This regulatory leniency, coupled with better-established offtake markets, improves the economic viability of tire pyrolysis projects.
Process Integration and Scalability
Oil sludge pyrolysis is often integrated within refinery ecosystems as an in-situ waste minimization strategy. These systems are typically custom-built and embedded into broader petrochemical operations.
Tire pyrolysis plants, by contrast, are more modular and scalable. They are suitable for decentralized deployment near collection centers or urban waste management zones, making them more accessible to a wider range of operators.